The i8 is truly a different breed of automobile. Unlike traditional vehicles with integral body and frame construction, the plug-in hybrid sportscar is done in a different way, combining two separate parts.
They’re called modules and come together in what BMW calls LifeDrive. The Life module is the one that houses the occupants, the humans and stands atop the aluminum bit that’s called the Drive module. This later half houses the engine, powertrain and transmission alongside the battery and everything else needed to power and propel the car.

Since the Life module is made exclusively of Carbon Fibre Reinforced Plastic (or CFRP for short, a combination of plastic and carbon fibre) and the Drive module is mostly made of aluminum, the car manages to keep its weight in check, tipping the scale at just under 1,500 kg (3,306 lbs) despite housing a huge battery, two gearboxes and two engines.
When the assembly begins, though, the i8 is put together on a single line, where everything is put together. First, the aluminum chassis is fitted with the high-voltage battery and then equipped with the drivetrain and transmission units. The front axle (that is preassembled in Dingolfing) is then mounted alongside other structural parts and the entire car is going into the next step.

This is where the Life module is added to the mix already fitted with the specific requirements the customers ordered. The two modules are bonded together at only 4 points while also giving it the optimal amount of stiffness and strength.
In the next step, the car is painted and then run through comprehensive quality controls to make sure everything is up to par with BMW’s standards.
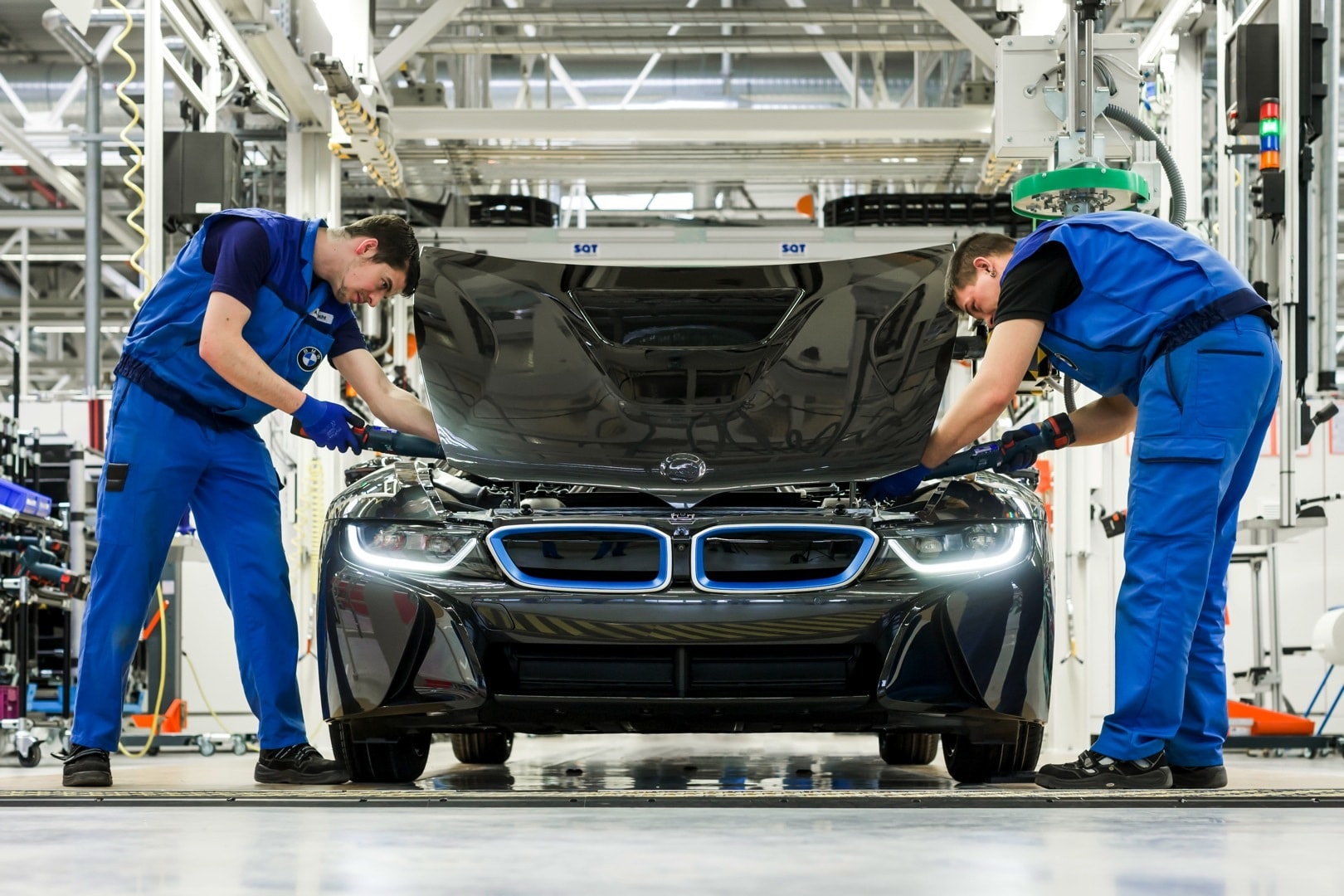
In total, it takes 14 work cycles to finish an i8 that add up to around 20 hours, which is half of what would be required in a conventional production process for such a car.
Of course, this is a minor part of a more complex process that begins with the production of CFRP in the US at the Moses Lake plant but we'll get into that another time.

Since the Life module is made exclusively of Carbon Fibre Reinforced Plastic (or CFRP for short, a combination of plastic and carbon fibre) and the Drive module is mostly made of aluminum, the car manages to keep its weight in check, tipping the scale at just under 1,500 kg (3,306 lbs) despite housing a huge battery, two gearboxes and two engines.
When the assembly begins, though, the i8 is put together on a single line, where everything is put together. First, the aluminum chassis is fitted with the high-voltage battery and then equipped with the drivetrain and transmission units. The front axle (that is preassembled in Dingolfing) is then mounted alongside other structural parts and the entire car is going into the next step.

This is where the Life module is added to the mix already fitted with the specific requirements the customers ordered. The two modules are bonded together at only 4 points while also giving it the optimal amount of stiffness and strength.
In the next step, the car is painted and then run through comprehensive quality controls to make sure everything is up to par with BMW’s standards.
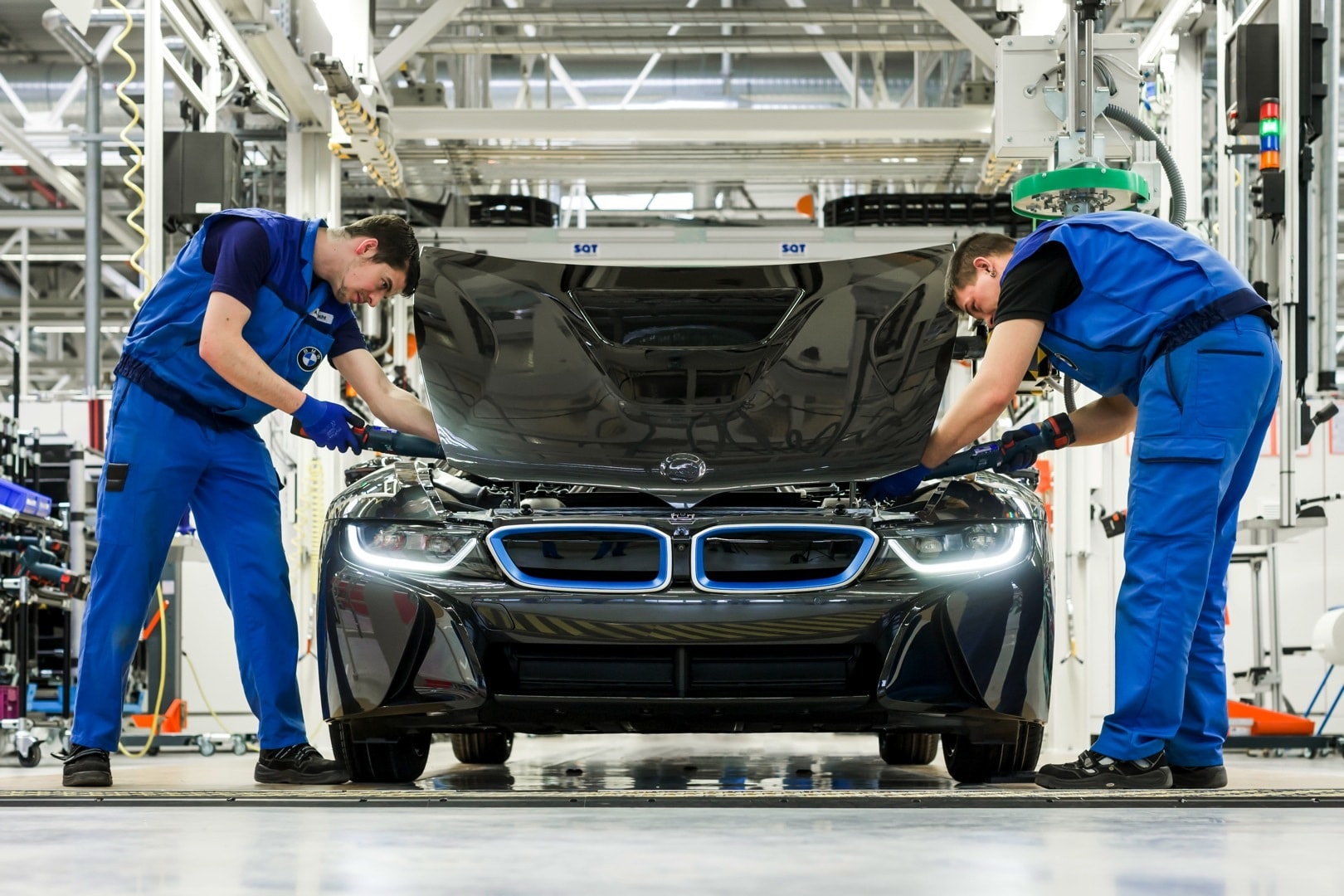
In total, it takes 14 work cycles to finish an i8 that add up to around 20 hours, which is half of what would be required in a conventional production process for such a car.
Of course, this is a minor part of a more complex process that begins with the production of CFRP in the US at the Moses Lake plant but we'll get into that another time.